The Ultimate Guide to Continuous Improvement: Tools and Methodologies
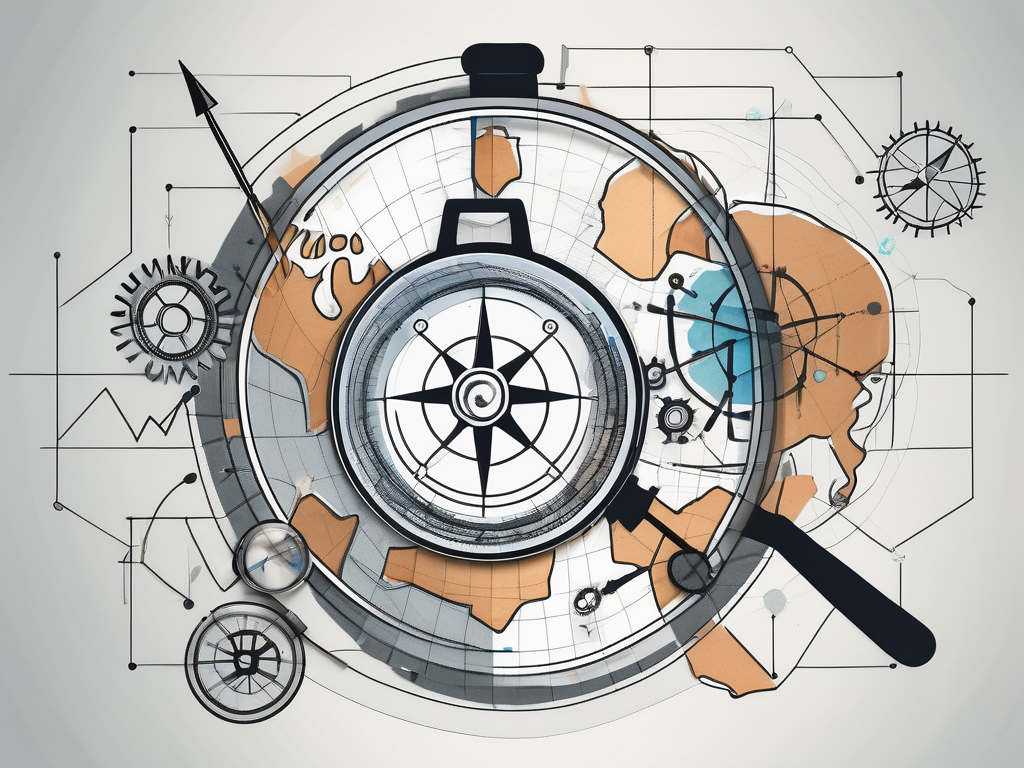
Continuous improvement is a critical aspect of achieving success in any organization. By constantly analyzing processes, identifying areas for enhancement, and implementing changes, organizations can stay ahead of the competition and continually improve their performance.
Unveiling the Essence of Continuous Improvement
Continuous improvement is not just a buzzword; it is a mindset and a systematic approach to enhancing processes, products, and services. At its core, continuous improvement emphasizes the importance of always striving for excellence and never settling for mediocrity.
To fully grasp the essence of continuous improvement, one must understand its core principles. These principles form the foundation upon which successful continuous improvement initiatives are built.
Continuous improvement is guided by principles that drive its success. These principles include:
- Culture of Learning: Embracing a culture of learning is fundamental to continuous improvement. It involves fostering an environment where experimentation, creativity, and innovation are encouraged.
- Data-Driven Approach: Continuous improvement relies on data to guide decision-making processes. Data analysis helps identify trends, patterns, and areas in need of improvement.
- Emphasizing Employee Involvement: Engaging employees in the continuous improvement process is crucial. By involving employees at all levels, organizations can tap into the insights and expertise of their workforce.
- Aligning with Organizational Goals: Continuous improvement initiatives should be aligned with an organization's strategic goals. This ensures that improvements are targeted and contribute to the overall success of the organization.
Exploring Different Continuous Improvement Tools
Continuous improvement relies on various tools and methodologies. These tools help organizations identify and address inefficiencies, bottlenecks, and opportunities for improvement. Some commonly used continuous improvement tools include:
- Pareto Analysis: Pareto analysis helps organizations prioritize improvement opportunities by identifying the most significant factors contributing to a particular issue.
- Flowcharts: Flowcharts provide a visual representation of processes, allowing organizations to identify areas of waste and inefficiency.
- Statistical Process Control (SPC): SPC is used to monitor and control processes, ensuring they operate within set parameters and drive continuous improvement.
- Root Cause Analysis: Root cause analysis helps organizations identify the underlying causes of problems, allowing them to implement targeted improvements.
The Role of Retrospectives in Continuous Improvement
Retrospectives play a crucial role in the continuous improvement process. These structured meetings provide an opportunity for teams to reflect on past performance, identify areas for improvement, and plan for future enhancements. By analyzing successes and failures, teams can continuously iterate and improve their processes.
Demystifying the Plan-Do-Check-Act (PDCA) Principle
The Plan-Do-Check-Act (PDCA) principle is a widely utilized continuous improvement framework. It involves four key steps: planning, executing, assessing, and acting on improvements. By following this iterative cycle, organizations can drive continuous improvement and ensure sustained success.
Delving into the 5 Whys Root Cause Analysis
The 5 Whys technique is a powerful tool for uncovering the root causes of problems. By repeatedly asking "why" and addressing the answers, organizations can peel back the layers to identify the fundamental causes of issues. This analysis enables targeted improvements and prevents recurring problems.
Embracing Kaizen and Kata for Continuous Improvement
Kaizen and Kata are two methodologies that promote continuous improvement. Kaizen focuses on incremental improvements made by all team members, while Kata emphasizes structured problem-solving. By embracing these methodologies, organizations can foster a culture of continuous improvement and empower employees to drive meaningful change.
The Impact of Lean Manufacturing on Continuous Improvement
Lean manufacturing is an approach that aims to eliminate waste and maximize efficiency. By eliminating non-value-added activities, organizations can enhance their processes and drive continuous improvement. The principles of lean manufacturing, such as just-in-time production and value stream mapping, are invaluable tools for organizations seeking to optimize their operations.
Total Quality Management (TQM) in the Context of Continuous Improvement
Total Quality Management (TQM) is a comprehensive approach that focuses on meeting customer expectations and continuously improving organizational processes. TQM emphasizes employee involvement, continuous learning, and a commitment to quality. By integrating TQM principles into their continuous improvement initiatives, organizations can achieve sustainable improvements and exceed customer expectations.
Unpacking the Agile Approach to Continuous Improvement
The agile approach, commonly used in software development, can also be applied to continuous improvement. Agile methodologies, such as Scrum and Kanban, promote iterative and flexible improvement processes. By breaking down work into manageable tasks and delivering incremental value, organizations can adapt quickly to changing circumstances and drive continuous improvement at a rapid pace.
Navigating the Kanban Method for Continuous Improvement
Kanban is a visual management system that helps organizations visualize workflow and identify bottlenecks. By limiting work in progress and focusing on completing tasks, organizations can drive continuous improvement and ensure smooth operations. Kanban provides a transparent and flexible approach to managing work and enhancing productivity.
Maximizing the Benefits of Continuous Improvement
While understanding the tools and methodologies of continuous improvement is essential, maximizing the benefits requires a comprehensive approach. Organizations must focus on key areas that can be enhanced through continuous improvement initiatives.
Boosting Operational Efficiency through Continuous Improvement
Operational efficiency is a critical factor in achieving success. Continuous improvement initiatives can streamline processes, eliminate waste, and improve productivity. By identifying and addressing inefficiencies, organizations can optimize their operations and gain a competitive advantage in the market.
For example, a manufacturing company implemented a continuous improvement program that involved analyzing their production line. They discovered that certain machines were causing bottlenecks, leading to delays and decreased efficiency. By reorganizing the layout and investing in new equipment, they were able to increase their production output by 20% and reduce lead times by 30%. This improvement not only enhanced their operational efficiency but also resulted in higher customer satisfaction and increased profitability.
Fostering Enhanced Employee Engagement via Continuous Improvement
Engaged employees are more productive, innovative, and committed to the organization's success. Continuous improvement provides a platform for employees to contribute their ideas, identify improvement opportunities, and take ownership of the process. By fostering a culture of continuous improvement, organizations can tap into the collective knowledge and expertise of their workforce.
One way to foster enhanced employee engagement is through regular improvement workshops or brainstorming sessions. These sessions allow employees from different departments to come together and share their perspectives on how to improve processes or solve problems. By involving employees in the decision-making process, organizations not only benefit from their valuable insights but also create a sense of ownership and empowerment among the workforce.
Strategies for Reducing Waste through Continuous Improvement
Waste is a significant barrier to efficiency and profitability. Through continuous improvement initiatives, organizations can identify and eliminate various forms of waste, such as overproduction, defects, and excess inventory. By reducing waste, organizations can optimize their resources, improve quality, and reduce costs.
One effective strategy for reducing waste is implementing the 5S methodology, which focuses on organizing the workplace and eliminating unnecessary items. By creating a clean and organized work environment, organizations can minimize the time wasted searching for tools or materials, improve safety, and enhance overall efficiency. Additionally, implementing lean manufacturing principles, such as Just-in-Time (JIT) production, can help organizations reduce inventory levels and eliminate the costs associated with storing excess materials.
The Financial Impact: Cost Reduction through Continuous Improvement
Continuous improvement can have a significant financial impact on organizations. By identifying and addressing inefficiencies, organizations can reduce costs and improve profitability. Cost reduction through continuous improvement can be achieved through various strategies, such as process optimization, waste reduction, and value stream mapping.
For instance, a service-based company implemented a continuous improvement program that focused on optimizing their customer support process. By analyzing customer inquiries and identifying common issues, they were able to develop standardized solutions and train their support team accordingly. As a result, the company experienced a 40% reduction in average handling time per inquiry, leading to significant cost savings and improved customer satisfaction.
Continuous improvement is not a one-time project; it is an ongoing journey towards excellence. By understanding the core principles, exploring different tools and methodologies, and focusing on maximizing the benefits, organizations can embark on a path of continuous improvement and drive sustainable success.