The Ultimate Guide to Understanding Quality Assurance vs. Quality Control
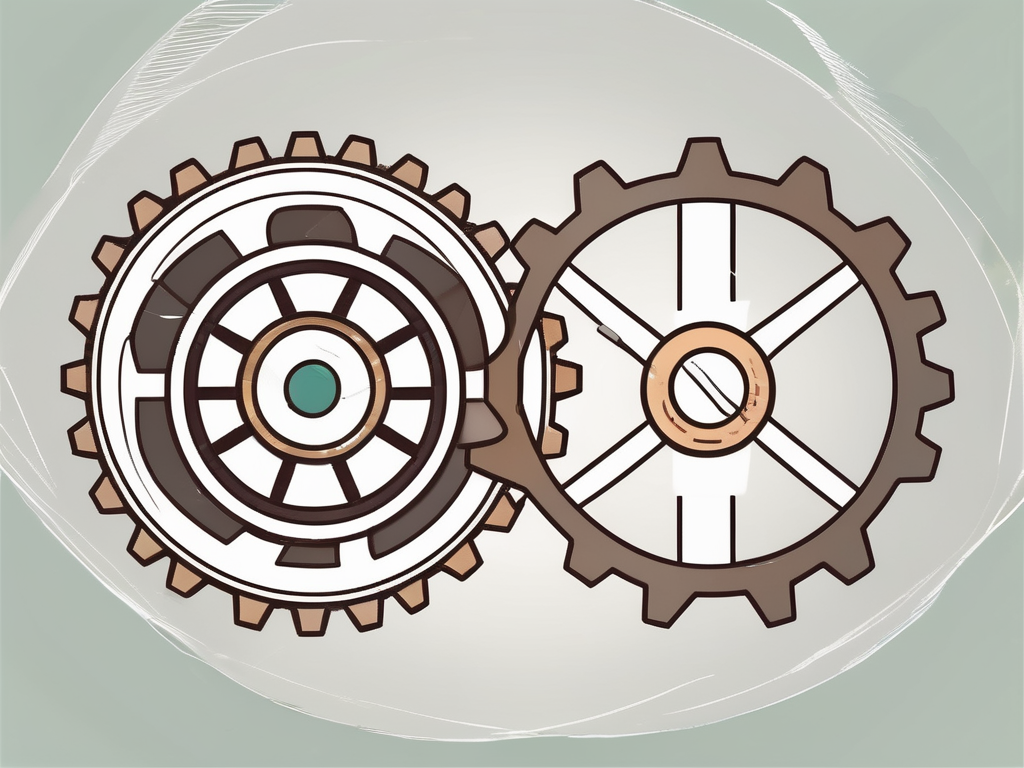
Quality assurance (QA) and quality control (QC) are two essential components of the production process. While they are often used interchangeably, they serve distinct purposes. Understanding the differences between these two concepts is crucial for any organization striving to deliver exceptional products and services consistently.
Understanding Quality Assurance
Quality assurance refers to the systematic processes and activities implemented to ensure that products or services meet specified quality requirements. By incorporating customer feedback, organizations can optimize their QA processes and enhance customer satisfaction.
Incorporating Customer Feedback for Quality Assurance
Customer feedback is a valuable source of information for organizations looking to improve their products or services. By actively listening to customers, businesses can identify areas for improvement and implement effective QA measures to address these concerns. This iterative process allows organizations to continuously enhance their products and meet customer expectations.
Ensuring Product Features Meet Quality Standards
QA also involves verifying that product features align with the quality standards set by the organization. Through rigorous testing and analysis, organizations can identify any deviations or deficiencies and take corrective measures. This ensures that all products meet the desired quality levels and function as intended.
Validating Quality Through Control Measures
QA is not limited to pre-production processes; it extends throughout the entire product lifecycle. Control measures are implemented during production to validate the quality of the final output. These measures can include inspections, audits, and process controls to monitor and ensure compliance with quality standards. By regularly assessing the production process, organizations can maintain consistent quality levels.
Addressing Non-Conformities in Quality Assurance
Despite careful planning and implementation of QA measures, non-conformities can still occur. Whether it's a defective component or a process failure, organizations must have strategies in place to address these issues swiftly and effectively. Root-cause analysis and corrective actions are key components of QA, enabling organizations to identify the source of non-conformities and prevent recurrence.
Moreover, organizations can also employ preventive measures to minimize the occurrence of non-conformities. This can include implementing robust quality control systems, conducting regular training programs for employees, and fostering a culture of continuous improvement. By taking a proactive approach, organizations can reduce the likelihood of non-conformities and ensure a higher level of quality in their products or services.
Furthermore, effective communication plays a crucial role in quality assurance. Clear and concise communication channels between different departments and stakeholders help in aligning everyone's understanding of quality requirements. This ensures that all parties involved are working towards the same goal and helps in avoiding misunderstandings or misinterpretations that could compromise the quality of the final product.
Mastering Quality Control Techniques
Quality control focuses on ensuring that the products and services meet the desired quality standards. It involves monitoring, measuring, and controlling various parameters to minimize defects and maintain consistent quality.
Setting Quality Standards for Effective Control
Before implementing quality control measures, organizations must establish clear quality standards for their products or services. These standards act as benchmarks against which the organization can measure its performance. By setting specific, measurable goals, organizations can effectively monitor and control quality throughout the production process.
For example, a clothing manufacturer may set quality standards that include criteria such as stitching precision, fabric durability, and colorfastness. These standards ensure that each garment meets the desired level of quality and meets customer expectations. By defining these standards, the manufacturer can consistently deliver high-quality products to its customers.
Making Focused Decisions in Quality Control
Quality control requires making informed decisions based on data analysis. By collecting and analyzing relevant data, organizations can identify patterns, trends, and potential areas for improvement. This data-driven approach enables organizations to make informed decisions to optimize their quality control processes.
For instance, a food processing company may collect data on various parameters such as temperature, pH levels, and microbial counts during the production process. By analyzing this data, the company can identify any deviations from the desired quality standards and take corrective actions. This proactive approach ensures that the final product meets the highest quality standards and minimizes the risk of contamination or spoilage.
Analyzing and Reviewing Quality Control Results
Regular analysis and review of quality control results are essential to assess the effectiveness of control measures. By examining performance data, organizations can identify opportunities for improvement, implement corrective actions, and enhance quality control processes. Continuous monitoring and evaluation help maintain consistent quality levels and drive continuous improvement.
For example, a software development company may conduct regular code reviews to ensure the quality of their software products. By analyzing the code, identifying any coding errors or inefficiencies, and providing feedback to the developers, the company can continuously improve the quality of their software. This iterative process of analysis and review helps the company deliver reliable and bug-free software to its clients.
Utilizing Feedback for Continuous Quality Improvement
Feedback plays a vital role in quality control. Whether obtained from customers, employees, or other stakeholders, feedback provides valuable insights into the quality of products and services. By actively seeking and leveraging feedback, organizations can identify areas for improvement, implement changes, and continuously enhance their quality control processes.
For instance, a customer service department may regularly gather feedback from customers through surveys or direct interactions. By analyzing this feedback, the department can identify any recurring issues or areas where customer satisfaction can be improved. Based on this feedback, the department can implement training programs for employees, update processes, or introduce new technologies to enhance the quality of customer service.
Overall, mastering quality control techniques requires a systematic approach that includes setting clear standards, making data-driven decisions, analyzing results, and utilizing feedback. By continuously striving for improvement, organizations can ensure that their products and services consistently meet the highest quality standards, resulting in customer satisfaction and business success.
Real-World Applications of Quality Assurance
Quality assurance practices are applicable in various industries to ensure the delivery of high-quality products and services. Let's explore some real-world examples of QA implementation.
Ensuring Security Through Quality Assurance Practices
In the realm of cybersecurity, quality assurance plays a crucial role in ensuring the security and reliability of software applications. By implementing rigorous QA processes, organizations can identify vulnerabilities, test security controls, and prevent potential breaches. QA measures such as penetration testing and code reviews help uncover security loopholes and ensure that software applications meet the highest security standards.
For example, imagine a company developing a mobile banking application. Through quality assurance practices, the development team can conduct extensive testing to ensure that the application is secure from potential hacking attempts. They can simulate various attack scenarios, analyze the application's response, and make necessary improvements to enhance its security. By prioritizing quality assurance, the company can provide customers with a secure platform for their financial transactions, instilling trust and confidence.
Maintaining Food Safety Standards with Quality Assurance
In the food industry, QA processes are paramount to maintaining safety and quality standards. From farm to fork, rigorous QA measures are implemented to ensure that food products are safe for consumption. This includes regular inspections, thorough testing, and adherence to hygiene protocols. By prioritizing quality assurance, organizations can prevent foodborne illnesses and safeguard consumer health.
Consider a large-scale food manufacturing company that produces canned goods. Through quality assurance practices, the company can implement stringent quality checks at every stage of the production process. From inspecting raw materials for contaminants to conducting microbiological tests on the final products, quality assurance ensures that the canned goods meet the highest food safety standards. By doing so, the company can protect consumers from potential health risks and maintain its reputation for delivering safe and high-quality products.
Implementing Quality Assurance in Design Processes
In the field of product design, quality assurance plays a critical role in ensuring that products meet the desired standards. QA in design processes involves rigorous testing, prototyping, and analysis to validate product performance, functionality, and reliability. By implementing quality assurance from the initial design stage, organizations can identify and rectify any design flaws, resulting in superior, high-quality products.
Take, for instance, an automotive company developing a new electric vehicle. Through quality assurance practices, the company can conduct extensive testing on various components, such as the battery, motor, and charging system. By analyzing the performance and reliability of these components, the company can make necessary improvements to ensure that the electric vehicle meets safety standards and performs optimally. Quality assurance in the design process helps the company deliver a cutting-edge electric vehicle that exceeds customer expectations.
Practical Examples of Quality Control
Quality control techniques are implemented in various industries to prevent defects and ensure consistent quality. Let's examine some practical examples of quality control in action.
Quality Control in Fast-Moving Consumer Goods Industry
In the fast-moving consumer goods (FMCG) industry, quality control is crucial to maintain product integrity and consumer satisfaction. From manufacturing to distribution, quality control measures are implemented at every step of the supply chain. This includes regular inspections, product testing, and quality checks to identify any defects or deviations from the desired standards. By implementing robust quality control measures, FMCG companies can ensure that their products meet customer expectations and comply with regulatory requirements.
One specific example of quality control in the FMCG industry is the use of statistical process control (SPC) techniques. SPC involves monitoring and controlling the production process through statistical analysis to ensure that it operates efficiently and produces products that meet quality standards. By collecting and analyzing data at various stages of production, FMCG companies can identify trends, detect any deviations from the norm, and take corrective actions promptly to maintain product quality.
Moreover, quality control in the FMCG industry also extends to packaging and labeling. Ensuring that the packaging materials meet safety standards, are free from defects, and accurately represent the product inside is essential for consumer safety and satisfaction. Quality control measures in packaging include visual inspections, barcode scanning, and compliance checks to guarantee that the right products are packaged correctly and reach consumers in optimal condition.
In conclusion, quality assurance and quality control are vital components of any organization's quest for customer satisfaction and product excellence. While quality assurance focuses on implementing processes and addressing non-conformities, quality control aims to maintain consistent quality through monitoring and control measures. By understanding and implementing both QA and QC techniques effectively, organizations can ensure that their products and services consistently meet or exceed customer expectations, resulting in long-term success and customer loyalty.